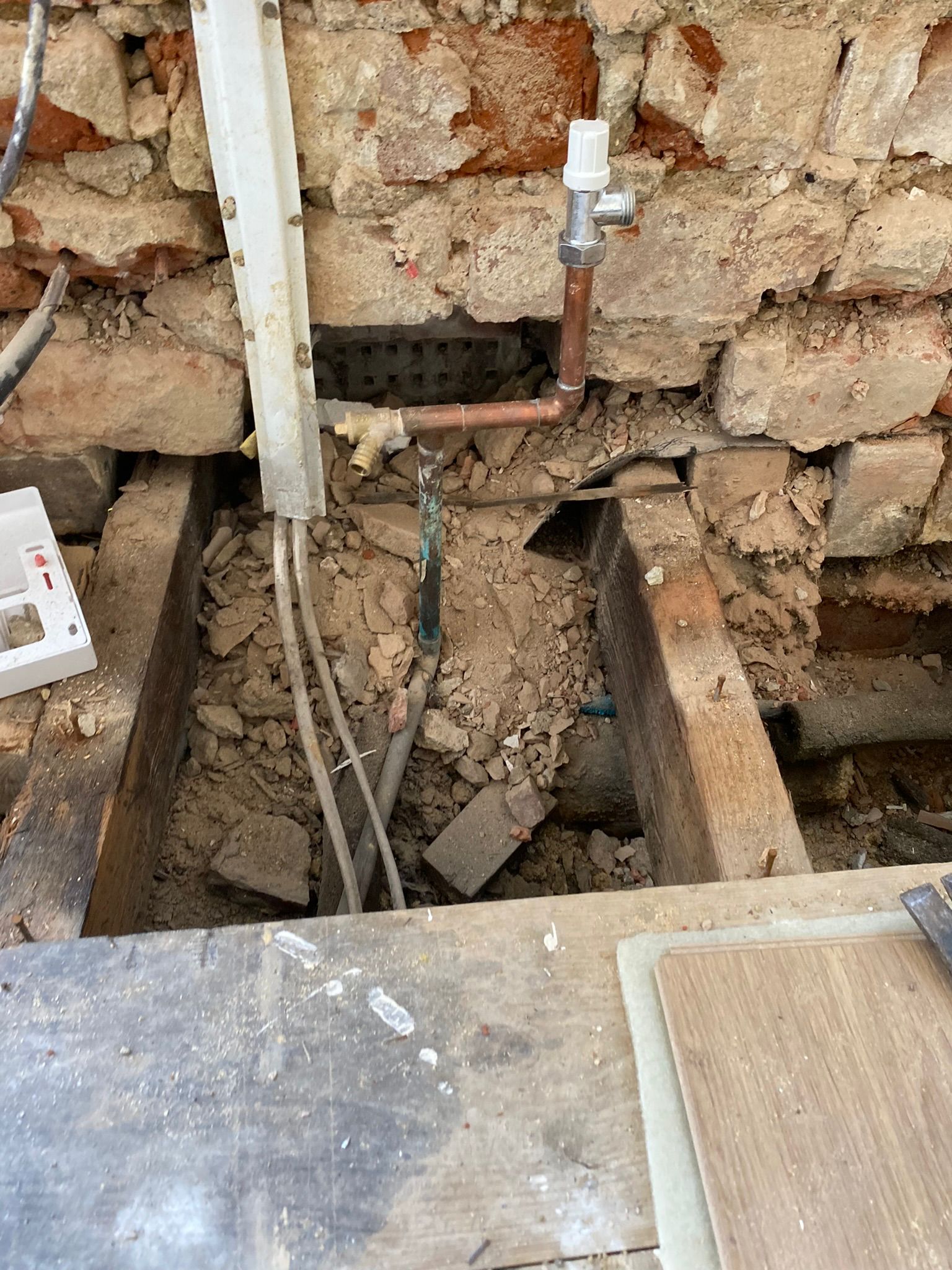
Location: Caversham, Reading
Type of property: Brick built c 1890, mix of solid and suspended wood flooring
Services used:
Materials Used:
Problem: Our damp surveyor visited the unoccupied property to carry out inspection of internal structural walls, the roof void and suspended wood flooring. Upon inspection using an electronic moisture meter it was found that moisture had reached an average height of 500mm above the floor level in the front room, middle room and kitchen areas. The moisture profile as well as the visual evidence indicated that the cause of the dampness was due to the wall plaster going down to the wall/floor junction and therefore bridging any existing damp proof course. The ingress of groundwater into the plaster also left salt deposits in the plaster, which were at risk of attracting further dampness from the surrounding atmosphere of the room. As the survey continued, other internal walls were found to be damp to the full height, the cause of which was determined as an abutting wall from the garden meeting the external wall surface. Later on, as our surveyor continued outside the property, it was found that the old airbricks were deteriorated, and the surrounding ground was too high to prevent run-off rainwater entering the subfloor void and timbers. This was determined to be the cause of the dampness in the suspended flooring and associated walls. Airbricks are essential to allow the proper ventilation of water and vapour from the subfloor void, which in turn ensures the timbers remain relatively dry. We recommended the replacement of the old airbricks with modern plastic versions and the removal of some ground around the recesses. This would improve the airflow by up to 70%. We also carried out a timber inspection in the roof void where we found no cause for concern and found a window lintel that needed replacing.
Works completed: Protection of all surfaces in the area where work was to be carried out. Skirting boards removed and plaster removed to various heights in rooms indicated on the surveyors report. Installation of chemical damp proof course Installation of 3mm Delta mesh membrane to various heights and areas Replaster using plasterboard or lightweight backing depending on wall thickness Replaster with skim finish and reinstate newly treated skirting boards Cutting back of damp floor joists and replacement of wall plates and joist ends Relaying existing flooring Reduction of ground level in accordance to recommendations for subfloor ventilation Installation of new airbricks NB: The damp proof course, membrane and plastering is guaranteed for a period of ten years.
Before
During
After